Pulsodyne SFOATM
pulsejet engine project photos:
by Larry Cottrill
This photo shows the SFOA engine raw materials lined up right beside the
lathe-finished ready-to-weld pieces. Raw materials (back row from left to right) are:
12 gram CO2 cylinder (nose cut & filed as shown to fit point of set screw),
5/8-18 set screw, 5/8-18 hex nut, CO2 cylinder, and 3/8 in. (nom.) galvanized steel
pipe (12 inch length). Finished pieces (front row, left to right): intake body
(set screw welded to cylinder neck end, drilled out and faced), 9/32 inch steel ball
valve body, 5/8-18 lock ring (turned from hex nut), 5/8-18 threaded sleeve (turned
from same nut), folded-washer-and-ball valve stop/bluff body, ignition chamber
(turned from CO2 cylinder) and tailpipe (turned from pipe). NOTE: In reality, only
one CO2 cylinder is needed to form both the intake bell and the ignition chamber;
the extra cylinder shown at the front end is an attempt to more clearly illustrate
the development of raw steel to finished pieces. The CO2 cylinders are 3/4 inch
(approx. 19mm) OD. |
|
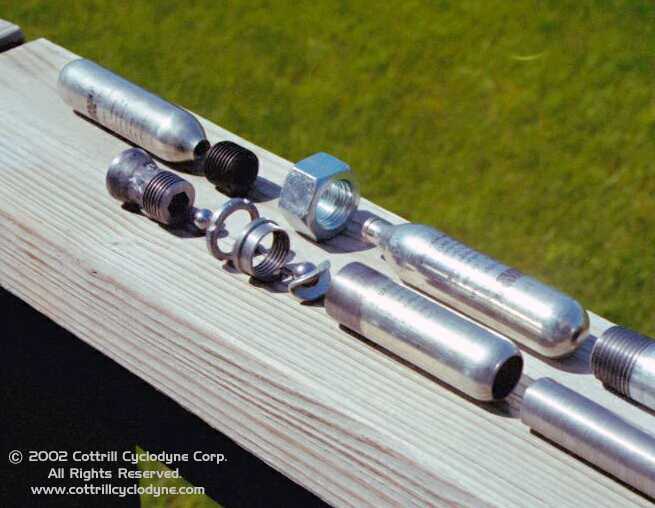 |
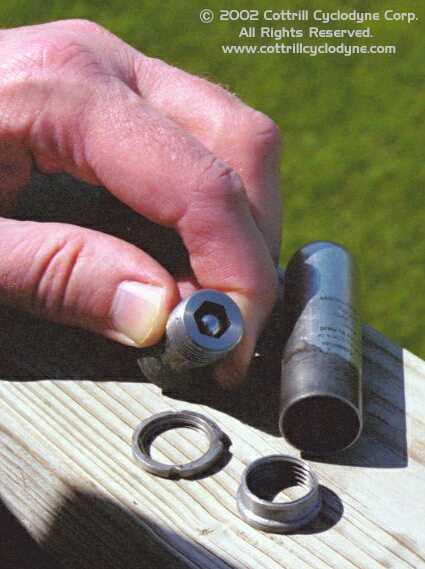 |
This detail shot shows the aft end of the intake body with the 9/32 inch steel ball
resting in place inside its hexagonal track, the lock ring (the ring with hand-filed notches
in the outer rim), the threaded insert and the ignition chamber front end into which
the insert will be welded. |
|
The aft end of the ignition chamber (turned out to fit the tailpipe) and the front end of
the tailpipe (note slight 'shelf' turned around the front edge). Made in this way, the pipe 'sockets'
into the chamber rear aperture slightly, but cannot slide through into the interior --
the fit is essentially self-aligning. The finished pipe wall thickness is approx.
1/16 inch (1.5mm); the pipe ID is approx. 1/2 inch (13mm). |
|
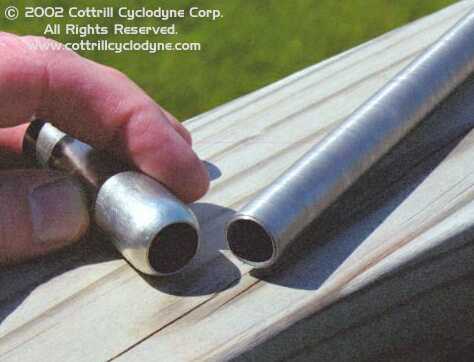 |
This shot shows how the tailpipe and ignition chamber are jigged for welding. A straight
piece of small steel angle is used. First, a spare CO2 cylinder (must be perfectly
identical to the raw cylinder used for the chamber) is clamped in place at the right end.
The aft end of the pipe is placed on the cylinder neck. Finally, at the left, the aft
end of the chamber is slid onto the specially turned front end of the pipe, and clamped --
the pipe is held in perfect alignment between the two cylinders. A couple of tack welds
will be made between chamber and pipe; then, the clamp on the chamber will be loosened
and the assembly rolled 180 degrees and re-clamped as before, and a couple more tack
welds will be made. Finish welding can then be done with the assembly removed from the
jig, with the tack welds preserving the alignment while welding. |
|
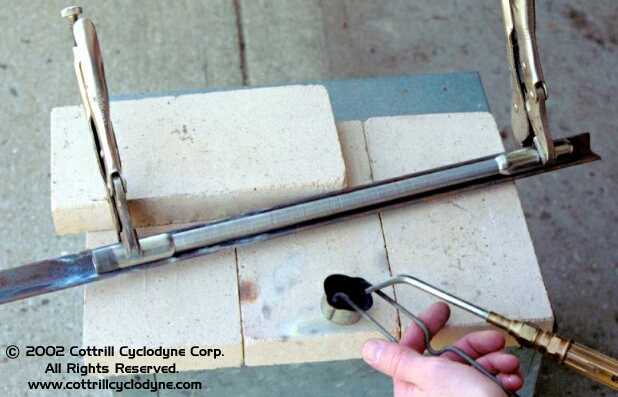 |
These two shots show the tail end and front end of the fully-welded sleeve and stop ball
assembly, ready to slip into the front of the chamber, which appears at the left in both
photos. Note in the top photo how the side weld has been smoothed off by filing to allow
the sleeve to slide easily into the chamber wall. [Compare this to the geometry shown in
the second drawing at the top of the page.]
Photos Copyright 2003 Cottrill Cyclodyne Corporation |
|
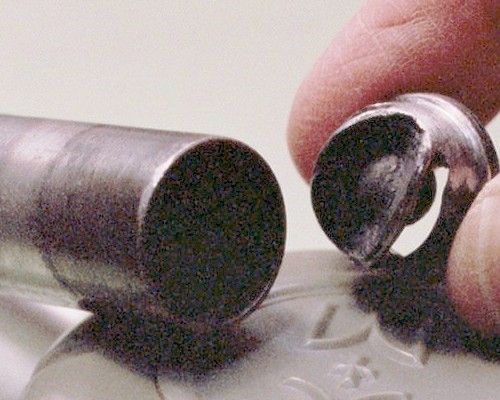 |
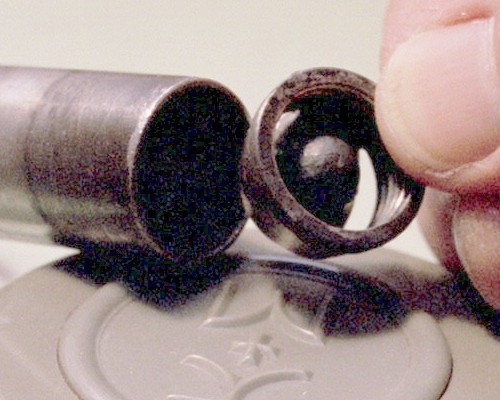 |
The finished state of the front end of the chamber, with the ball stop and flameholder assembly
fitted into the chamber and welded into place, is shown in this photo. The valve ball
can be seen resting in the hexagonal channel in the rear of the intake body.
Photo Copyright 2003 Cottrill Cyclodyne Corporation |
|
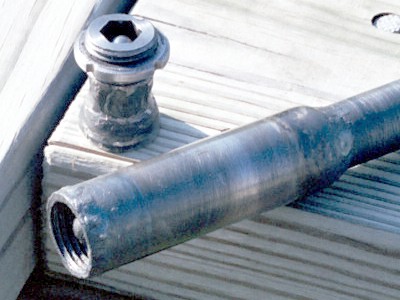 |
A "fully assembled" view looking into the front end of the intake body, which has been threaded in and locked with
the lock ring. The valve body is run in until the ball has just a few thousandths of an inch of free
play between its seat and the stop behind it -- the exact setting for good operation will need to be
determined experimentally. The steel valve ball is just visible as a tiny reflection of blue sky at the
far end of the venturi throat in this photo.
Photo Copyright 2003 Cottrill Cyclodyne Corporation |
|
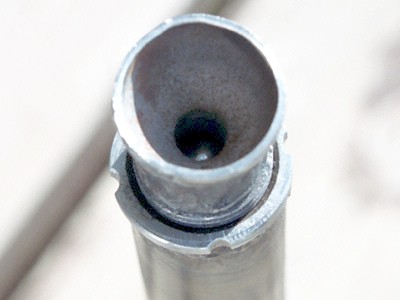 |
SPECIAL THANKS to my friend (and brilliant artist!) Jim Russell (Jim Russell Design,
Des Moines, Iowa, USA), for graciously allowing me to use his turning lathe to generate
the parts shown. His assistance was invaluable, especially since this was the first
time I had touched a metal-turning lathe in about thirty-five years! |
All film processing and negative
scanning for this page was done by
Multi Media Imaging
1526 Walnut Street
Des Moines, Iowa USA 50309
515-309-3456
www.multi-media-inc.com
|
|